Modern & intelligently designed.
Since the foundation of Medistri in 2006, we have been highly focused on offering the solutions that will benefit our customers, our community and the future of our planet. We believe that the downside of Ethylene Oxide can be eliminated when working with modern and intelligently designed operations.
We have invested our resources in finding smarter systems, protocols & validation methods to reduce, optimise and eliminate ethylene oxide emissions. Although there are local and federal regulations that have been put in place for such purposes, we believe in setting up even higher internal standards to ensure the health and safety of our communities and future generations.
Low-Carbon Design.
Using an attentive selection of materials, suppliers, tighter tolerances efficiency, and superior operational efficiency, we will develop solutions and operations less carbon-intensive.
Renewable Green Electricity.
Starting 2022, we will achieve 100% renewable energy generated in Switzerland (99.8% hydropower, 2% Solar - based on contractual agreement) in our facilities and work with our suppliers' network to establish aligned environmental & community goals.
Tracking our Carbon Footprint, Pallet by Pallet.
At Medistri, we take responsibility for our services throughout their entire cycles—from sourcing materials, managing processes to forwarding the products to our customers. We focus on the areas where we can make the biggest difference for our planet: reducing our impact on climate change, conserving important resources and using safer materials.
In December of 2022, Medistri’s CO2 Report was completed by an external auditor and it has been generated in accordance with the ISO 14064 standards and the Greenhouse Gas Protocol principles. With this report, we're excited to announce that Medistri is the first Contract Sterilisation Company in the industry to measure and calculate its carbon footprint.
This marks a significant milestone in our commitment to sustainability and reducing our impact on the environment. For the first time in our industry, by carefully tracking and analyzing our energy usage, transportation, waste and other environmental factors, Medistri's CO2 Report gives our customers exact data on the average CO2 consumption per pallet that goes through our EO Sterilisation process.
Gas treatment technology.
We’ve installed complex, leading-edge, high-performance gas treatment technology systems. Our systems are in full compliance with local and federal legislation and they allow for an almost 100% complete reduction of EO emissions.
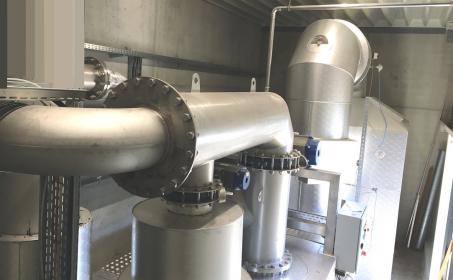
Fundamentally, our two-step technology forces the gas to pass through our Peak Shaver followed by an injection of the gas residuals through our Catalytic Burner. Our Peak Shaver reduces gas concentration and our Catalytic Burner eliminates the gas.
Energy efficiency.
We reduce carbon emissions through our operations and in our value chain by exploring solutions to reduce carbon use, through efficient design and construction.
We’ve accomplished 3 large investments to improve our processes and allow ourselves to operate our facilities 24/7 and improve upon the already-fully respected environmental rules as well as at the complete safety of our employees.
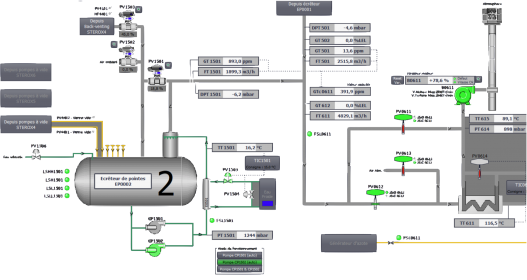
We’ve installed complex, leading-edge, high-performance gas treatment technology systems. Our systems are in full compliance with local and federal legislation and they allow for an almost 100% complete reduction of EO emissions.
We’ve accomplished 3 large investments to improve our processes and allow ourselves to operate our facilities 24/7 and improve upon the already-fully respected environmental rules as well as at the complete safety of our employees.

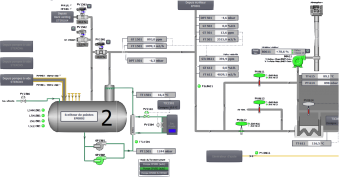
Comparing the Two Approaches.
At Medistri, we’ve also invested our resources in order to offer a better alternative to the traditional sterilization method.
We’ve popularised & offered a smarter alternative to the market called the “ Biological Indicator/ Bioburden Approach”. Let’s compare it to the traditional “Overkill Approach B”.
Overkill Approach B.
The traditional Method Overkill Approach B is based on the performance of 3 half-cycles with total kill of Biological indicators and 1 short cycle with some growths.
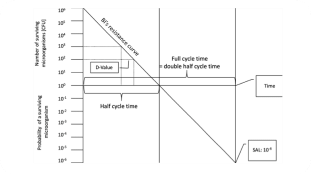
- Conservative Method.
- Already known in the market, easy to defend and explain to customers and auditors.
- The cost of validation is known.
- The quantity of EO gas used is too high as base on Biological indicators 10^(-6) with high contamination.
- Cycle length too long: It can reach up to 20 hours for certain products with additional degassing time.
- Not environmentally friendly, Not a sustainable process.
Biological Indicator/ Bioburden Approach A.
Biological Indicator/ Bioburden Approach A requires that the bioburden stays constant over time and less resistant than the biological indicators used. For completing this approach several cycles with different exposure times are performed in order to find the lethal rate.
- Cycle length is shorter as there is less aeration time because less gas is used.
- EO gas quantity will be reduced as bioburden is lower than the biological indicators
- The residue in the products will be decreased, faster release of products- Costs of cycle decreases.
- Sustainable & environmentally friendly method.
- During this method by the performance of several cycles comparison of products and identifying the worst-case product could be clearly demonstrated.
- Requires good control of the bioburden trend.
- Not fully known in the market.
- More cycles to perform.
- The validation price might be higher than the traditional overkill method.
Achieve your environmental targets.
Wether you work in the medical device industry, the aero-spacial industry, or any other industry were EO sterilization is required, we advice you to consider reducing the usage of gas in your sterilization process. The usage of Ethylene Oxide can not be 100% eliminated but can be greatly reduced through different smarter validation methods and control of the process.The markets are moving towards more sustainable processes. Using less gas, having faster cycles with less residuals allows you to become a forward-thinking market leader.
For the first time in the industry, by carefully tracking and analyzing its energy usage, transportation, waste and other environmental factors, Medistri's CO2 Report gives its customers exact data on the average CO2 consumption per pallet that goes through our its sterilisation process.
The complete report will be made available to Medistri’s on-site auditors.
Medistri will gladly help you with training and certifying your team to become competent with this validation process which will lead to greater competitive advantage. It is easy to see a future where these changes will ultimately be required by our regulatory authorities. Being first compounds very quickly to increased benefits for all your stakeholders.
The report has been generated in accordance with the ISO 14064 standards and the Greenhouse Gas Protocol principles. With this report, we're excited to announce that Medistri is the first Contract Sterilisation Company in the industry to measure and calculate its carbon footprint.